Empire State Building History
The Empire State Building was built during 1930 and 1931, primarily as a response to the growing demand for office space in New York City and the competitive drive to construct the world’s tallest skyscraper to symbolize American economic power and engineering prowess.
Construction began on March 17, 1930, during the peak of the Great Depression, and remarkably, the skyscraper was completed in just 1 year and 45 days.
Built under the guidance of John J. Raskob and Al Smith, this towering structure initially struggled to find tenants, earning the nickname “The Empty State Building.” Today, the Empire State Building is a cultural icon and one of the most recognizable landmarks in the world, forever linked with the skyline of New York City.
Construction Facts
Beyond its cultural significance, the Empire State Building offers valuable insights into construction efficiency and management. Here are some fascinating construction facts:
- The project, the design, planning and construction of the Empire State Building took just 20 months from start to finish.
- 3,400 construction workers participated in the project.
- The building required 60,000 tons of steel, 10 million bricks, and 200,000 cubic feet of limestone and granite.
- The exterior of the Empire State Building is composed of 200,000 cubic feet of Indiana limestone and granite, 10 million bricks and 730 tons of aluminum and stainless steel.
- Construction moved at an impressive pace of 4.5 stories per week, using advanced techniques like prefabrication and a well-coordinated workforce.
- The total construction cost was $40.9 million at the time, which is equivalent to around $560 million today.
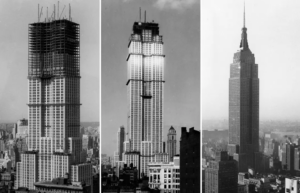
These extraordinary achievements underscore the remarkable level of precision, planning, and innovation that defined the construction of the Empire State Building. Yet, despite its success, the project faced numerous challenges along the way. Challenges that, with today’s modern project management tools, might have been addressed even more efficiently.
Project Management Challenges
The Empire State Building’s construction was a remarkable feat, but it wasn’t without its hurdles. Here are some of the key project management challenges faced:
1. Quick Project deadline
- The Empire State Building was completed in an astonishing 1 year and 45 days, far faster than the average 2-3 years it typically took to construct skyscrapers of a similar size at the time. For example, the Chrysler Building, in Manhattan, completed just before, took about 2 years.
- This incredibly tight deadline placed immense pressure on the construction team, requiring meticulous planning, synchronized schedules, and constant communication.
- At the time there was no modern technology to assist with real-time updates or task management tools. The team had to rely on manual coordination, increasing the risk of miscommunication and project delays.
2. Complex Supply Chain Logistics
- Managing the logistics for such a massive structure was another monumental task. The project required 60,000 tons of steel, 10 million bricks, and 200,000 cubic feet (about twice the volume of an Olympic-size swimming pool) of limestone and granite, all of which had to be delivered to a congested Manhattan worksite on time and within budget.
- Without the help of modern supply chain management tools, delays or mismanagement could occur causing costly interruptions, and there was no advanced technology to minimize errors or predict bottlenecks in the supply chain back in the 1930s.
3. Managing a Large Workforce
- At its peak, the construction employed 3,400 workers on-site daily. Assigning tasks, managing shifts, and ensuring efficient use of time was a significant challenge. The lack of modern communication and workforce management systems meant that everything was done manually, leaving room for inefficiencies and errors.
- Properly managing these teams was crucial to avoid safety risks and project delays. Mismanagement could easily lead to costly setbacks or worse, unsafe working conditions.
4. Safety Concerns
- The safety standards of the 1930s were not nearly as advanced as today. Workers often operated at extreme heights without proper safety gear, and the responsibility of maintaining protocols for 3,400 workers on such a fast-paced project was daunting.
- Despite these challenges, the project had a relatively low fatality rate of five deaths, but the inherent risks of working on a skyscraper without modern safety equipment made construction a dangerous endeavor.
5. Poor Communication
- In an era the 1930s, when society was without project management software, smartphones, or real-time updates, communication was one of the most difficult aspects of the Empire State Building’s construction. Coordinating between different teams, tracking project progress, and managing unexpected changes were all done through paper documentation, phone calls, and in-person meetings.
- This lack of instant communication often led to delays and made it much harder to adapt quickly to changes, slowing down decision-making and creating room for misalignment between teams.
6. Unpredictable Weather Conditions
- Working through New York’s unpredictable weather was another challenge, particularly during the winter and rainy seasons. Teams had to continue working in extreme conditions, which not only slowed progress but also introduced additional safety concerns.
- Without the ability to track weather changes in real time or adjust the construction schedule accordingly, the team had to constantly adapt on-site, often leading to delays and increased risks.
How a PMIS Could Have Improved the Construction Process
If the Empire State building was created today using a Project Management Information System these hurdles could have been solved and taken care of easier and faster. Here is how a PMIS could have improved the Empire State Building construction:
1. Supply Chain Optimization
- With PMIS, advanced tracking features would have ensured that materials arrived on time.
- It could have tracked material usage in real time, providing the project team with accurate forecasts of what was needed and when, minimizing wastage and supply shortages.
2. Real-Time Efficient Labor Management
- A PMIS optimizes workflow schedules by tracking productivity in real time, ensuring that each worker had specific tasks, and that no labor was wasted.
- This would have maximized efficiency and minimized costly delays by ensuring seamless coordination of the massive workforce.
3. Improved Risk and Safety Management
- A PMIS system could have dramatically improved risk management by sending out safety briefings, tracking incidents in real time, and ensuring compliance with safety protocols.
- This would have made it easier to enforce safety measures across the vast workforce, potentially saving lives and reducing accidents on site.
4. Streamlined Communication and Schedule Management
- In the 1930s, communication between teams was reliant on in-person meetings, handwritten notes, and phone calls. This slow inefficient method of communication could lead to miscommunication and delays.
- With a modern PMIS, project teams could communicate instantly through real-time messaging, keeping all workers informed of updates, task changes, and project milestones.
- These real-time updates could not only improve communication amongst others but also kept stakeholders and engineers up to date on real time progress.
5. Weather Monitoring
- PMIS offers real-time weather monitoring tools, allowing the construction team to track upcoming weather changes and adjust the schedule proactively.
- This could have minimized weather-related delays while ensuring the safety of the workforce during hazardous conditions.
6. Budget Management
- With a total cost of $40.9 million at the time (equivalent to about $560 million today), the Empire State Building’s budget was constantly being monitored, especially since the building was built during the Great Depression.
- PMIS could have tracked expenses in real time, alerting project managers if costs were going to go over budget and providing detailed cost forecasts.
- This could have allowed for better financial decision-making, reducing the risk of overruns and helping the project stay on budget.
7. Centralized Documentation
- During the Empire State Building’s construction, managing blueprints, contracts, and reports was done manually, increasing the risk of errors and inefficiencies.
- With a PMIS, all project documentation could have been stored in a centralized location, making it easier to track changes, ensure everyone had the most up-to-date plans, and reduce the administrative burden of managing complex documents.
While the great achievement of completing the building in just 1 year and 45 days was already an extraordinary feat, by integrating the power of PMIS, the process could have been even more efficient, faster, safer, and cost-effective.
How Could ATSER’s PMIS Help
While the Empire State Building was constructed without the advantages of modern technology, a tool like ATSER’s Project Management Information System (PMIS), “Manage-IT™” could have revolutionized the entire process. Manage-IT™ is designed to tackle the unique challenges of large-scale projects, streamlining workflows, optimizing budget management, and enhancing overall efficiency.
Here is How Manage-IT™ Features Could Have Made a Difference
a. Effortless Project Oversight with Administration Suite: Manage-IT™ equips construction managers with powerful tools to streamline tracking of every process, from budgets to timelines, in one centralized platform. Make smarter, faster decisions with real-time visibility across your projects.
b. Simplified Reporting & Payments with Construction Suite: ATSER’s PMIS simplifies your day-to-day tasks by automating daily progress reports, construction updates, and staff payment calculations—saving time while keeping your projects on track and within budget.
c. Seamless Team Collaboration with Real-Time Data & Communication: Manage-IT™ delivers real-time data sharing and instant communication, ensuring all teams are aligned with the latest project developments, reducing errors, and enhancing overall project coordination.
Here’s Why ATSER’s PMIS outperforms the competition:
1. Proven Success
- With over 30 years of experience, ATSER has been delivering tailored solutions that help architecture, construction, and engineering firms organize and centralize critical documentation. ATSER’s technology has consistently supported the execution of large projects, ensuring quality, organization, and efficiency every step of the way.
2. Real-Time Workflow
- Manage-IT™ provides real-time updates, giving project managers up-to-date insights into project progress, budget tracking, resource allocation, and more. With state-of-the-art real-time reporting, ATSER ensures projects run smoothly, reducing delays and improving decision-making.
3. Seamless Integration into existing platforms
- ATSER’s Manage-IT™ integrates effortlessly with other project management and financial tools, allowing teams to continue using their existing systems. This integration eliminates the need for lengthy retraining, saving both time and money, while enabling teams to work efficiently with tools they’re already familiar with.
4. Comprehensive support and Continuous Updates
- ATSER is committed to its clients by providing personalized customer support and consistently upgrading its systems to integrate new tools and features. With ATSER, you’ll consistently have access to the latest technology, guaranteeing that your projects receive advanced technical support.
Tackling a complex construction project? Discover how our PMIS can streamline your project management, optimize resources, and keep your team aligned from start to finish. Let our experts tailor a solution that fits your unique project needs and drives success.
Ready to boost efficiency? Connect with our Solutions Engineers today and see how we can help transform your next project, click here to reach out!